Company / Organisation
Focus
In order to bring real added value and achieve excellence, we focus on our core expertise (Engineering, project management, commissioning and services), and subcontract the manufacturing phases to qualified subcontractors and partners.
Not only this ensures high flexibility face to project requirements, but this also allows to deploy activity worldwide, as per client constraints (Logistics, local content, etc.). We entirely manage the interfaces and oversee every aspect of the project up to turnkey delivery, and full support.
Project management
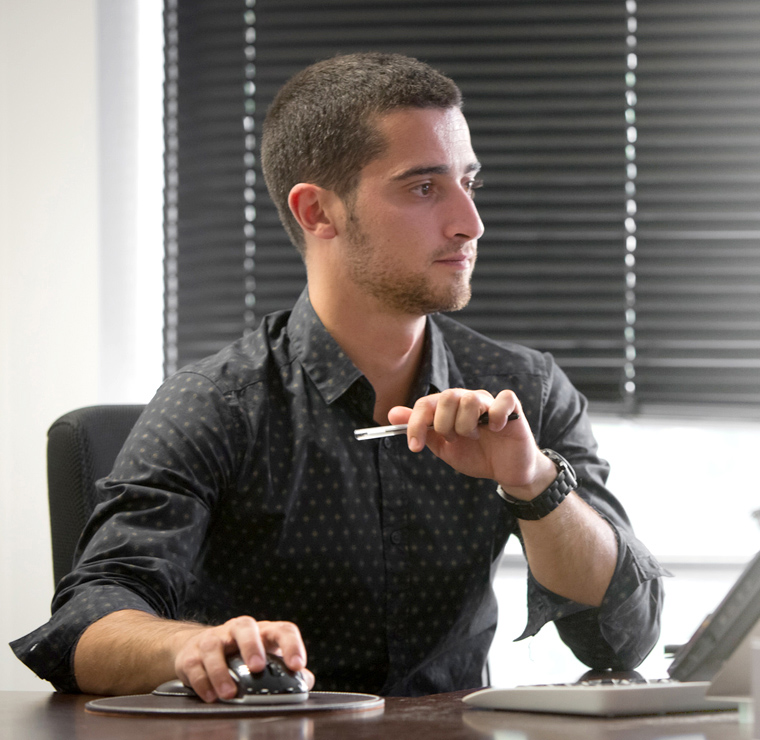
Project management.
Project management
A highly skilled Project Manager attends the client needs, and ensures that project goes smoothly on time and on budget, until turnkey delivery.
Engineering
Our solutions are developed 100% internally.
Our engineering team is split into two distinct yet closely related engineering offices:
Mechanical design and motorization (power and control) design, including hydraulics, electrics and automation (software).
We hold several patents in relation with linear winches, heavy lifting and fiber rope deployment winches (FRDS), and sustain R&D activity.
Manufacturing
Manufacturing of mechanical parts is entrusted to highly qualified subcontractors, selected for their excellence in processes such as welding, machining, heat treatment, and surface treatment.
Control command
Control command units (power and control, including PLC software) are developed either in-house or in partnership with suppliers, based on our detailed specification and functional analyses. Equipment are powered by electrical cubicles (VFD’s) or hydraulic power units (electric or diesel HPU).
In all cases, Kleyfrance retains full control, by defining the architecture and regulation loops, establishing detailed specifications, and running functional tests.
Assembly, commissioning, testing
Assembly, commissioning and testing of the equipment are performed by our teams in our 1500 m² premises located close to Nantes.
We regularly deploy our organization and teams around the globe to adapt to project requirements.
After sales services
Our product support office efficiently handles all logistics and human issues related to supply of spare parts and onsite support. Our site engineers are ready to go anywhere in the world on short notice for support, maintenance and operations. They hold all necessary documents to work either onshore or offshore (eg visas, medical certificates, BOSIET and HUET training certificates).
Project management
A highly skilled Project Manager attends the client needs, and ensures that project goes smoothly on time and on budget, until turnkey delivery.
Engineering
Our solutions are developed 100% internally.
Our engineering team is split into two distinct yet closely related engineering offices:
Mechanical design and motorization (power and control) design, including hydraulics, electrics and automation (software).
We hold several patents in relation with linear winches, heavy lifting and fiber rope deployment winches (FRDS), and sustain R&D activity.
Manufacturing
Manufacturing of mechanical parts is entrusted to highly qualified subcontractors, selected for their excellence in processes such as welding, machining, heat treatment, and surface treatment.
Control command
Control command units (power and control, including PLC software) are developed either in-house or in partnership with suppliers, based on our detailed specification and functional analyses. Equipment are powered by electrical cubicles (VFD’s) or hydraulic power units (electric or diesel HPU).
In all cases, Kleyfrance retains full control, by defining the architecture and regulation loops, establishing detailed specifications, and running functional tests.
Assembly, commissioning, testing
Assembly, commissioning and testing of the equipment are performed by our teams in our 1500 m² premises located close to Nantes.
We regularly deploy our organization and teams around the globe to adapt to project requirements.
After sales services
Our product support office efficiently handles all logistics and human issues related to supply of spare parts and onsite support. Our site engineers are ready to go anywhere in the world on short notice for support, maintenance and operations.
They hold all necessary documents to work either onshore or offshore (eg visas, medical certificates, BOSIET and HUET training certificates).